91 Club Car Service Manual
. 1997 MAINTENANCE SERVICE SUPPLEMENT DS GOLF CARS GASOLINE/ELECTRIC MANUAL NUMBER 1019345-04 PRINT CODE 0197C0398A. However, unique situations do sometimes arise when servicing golf cars. If it appears that a service question is not answered in this supplement or in the manual, you may write to us or contact a Club Car tech- nical service representative by phone at (706) 863-3000, ext.
CATIONS WHICH AFFECT THE STABILITY OF THE VEHICLE OR THE OPERATION THEREOF, WILL VOID THE WARRANTY. CLUB CAR, INC. RESERVES THE RIGHT TO CHANGE SPECIFICATIONS AND DESIGNS AT ANY TIME WITHOUT NOTICE AND WITHOUT INCURRING ANY OBLIGATION OR LIABILITY WHATSOEVER. Wysong shear 1010 manual. CONTENTS SECTION 1 - SAFETY SECTION 2 - VEHICLE SPECIFICATIONS Section 2 in this supplement supersedes Section 2 in the 1995-1996 DS Maintenance and Service Manual. SECTION 3 - GENERAL INFORMATION Use this supplement for current information on the subjects listed below. See Section 3 in the 1995-1996 DS Golf Car Maintenance and Service Manual for all other information.
SECTION 10 - UNITIZED TRANSAXLE AND GOVERNOR For gasoline vehicles only, Section 10 in this supplement supersedes Section 9 and Section 17 in the 1995-1996 DS Maintenance and Service Manual. General Information. Axle Shaft.Removing the Unitized Transaxle. Unitized Transaxle Disassembly. SECTION 13 - FE 290 ENGINE, CONTINUED: Engine Mounting Plate.Installation of Remaining Engine Components. Engine Removal.Engine Assembly.SECTION 14 - FUEL SYSTEM Use this supplement for current information on the subjects listed below.
Manual Rear Brake Assy. Motor - Powerdrive; On-Board Charger. Browse our online catalog to find the parts you need for your 1984-1991 Club Car Gas Golf Cart.
- View and Download Club Car Gasoline service manual online. Club Car recommends a. CHAMFERED INSIDE DIAMETER CHAMFERED INSIDE DIAMETER FIGURE 13-91 3.
- Golf Cart Repair Manuals for Gas and Electric Golf Cart Repair instructions. Club, EZGO and Yamaha Golf Cart manuals. Club Car Service Manual. EZGO Golf Cart Manual.
See Section 14 in the 1995-1996 DS Golf Car Maintenance and Service Manual for all other information. SECTION 20A - ELECTRICAL SYSTEM, POWERDRIVE SYSTEM 48 See 1995-1996 DS Golf Car Maintenance and Service Manual. SECTION 20B - ELECTRICAL COMPONENTS, POWERDRIVE SYSTEM 48 VEHICLE See 1995-1996 DS Golf Car Maintenance and Service Manual. SECTION 21A - ELECTRICAL SYSTEM, POWERDRIVE PLUS See 1995-1996 DS Golf Car Maintenance and Service Manual. SECTION 1 - SAFETY To insure the safety of those servicing Club Car DS Golf Cars, and to protect the vehicles from possible dam- age resulting from improper service or maintenance, the procedures in this manual must be followed. It is important to note that throughout this manual there are statements which are contained within boxes labeled DANGER, WARNING, or CAUTION.
General Safety Statements, Continued: WARNING. ONLY TRAINED MECHANICS SHOULD REPAIR OR SERVICE THIS VEHICLE. ANYONE DOING EVEN SIMPLE REPAIRS OR SERVICE SHOULD HAVE KNOWLEDGE AND EXPERIENCE IN GENERAL ELECTRICAL AND MECHANICAL REPAIR. FOLLOW ALL PROCEDURES EXACTLY AND HEED ALL WARNINGS STATED IN THIS MANUAL.
SECTION 2 - VEHICLE SPECIFICATIONS Club Car, Inc. Reserves the right to change specifications and design of either gasoline or electric vehicles at any time without notice and without obligation to make these changes on units previously sold. POWERDRIVE POWERDRIVE. POWERDRIVE POWERDRIVE SPECIFICATIONS SYSTEM 48 PLUS 36 VOLT GASOLINE ELECTRIC ELECTRIC ELECTRIC DIMENSIONS/WEIGHT 91-1/2” 91-1/2” 91-1/2” 91-1/2” Overall Length (232 cm) (232 cm) (232 cm) (232 cm) 47-1/4” 47-1/4” 47-1/4” 47-1/4” Overall Width (120 cm) (120 cm) (120 cm) (120 cm) 48”.
Service Manual should read as follows: PRE-OPERATION CHECKLIST Your CLUB CAR has been thoroughly inspected and adjusted at the factory, and also by your CLUB CAR distributor/dealer. However, upon arrival of your new CLUB CAR(s), you should become familiar with its con- trols and operation, and carefully inspect each vehicle to be satisfied that it is in proper working condition. SECTION 4 - PERIODIC MAINTENANCE It is important to implement and follow a Preventive Maintenance program for your vehicle(s). Preventive Maintenance consists of the regular performance of scheduled vehicle service and maintenance procedures, and is the only way to insure that the vehicle provides the safe, reliable, and economical service that it is designed to deliver. REGULAR INTERVAL SERVICE RECOMMENDED LUBRICANT PLACE Brake shaft bearings Dry Moly Lube - Club Car Part No. 1012151 Brake Linkage and Pivots Dry Moly Lube - Club Car Part No. 1012151 Quarterly by Owner Accelerator push rod pivots and Dry Moly Lube - Club Car Part No.
PERIODIC LUBRICATION SCHEDULE - ELECTRIC VEHICLES REGULAR INTERVAL SERVICE PLACE. RECOMMENDED LUBRICANT Brake shaft bearings Dry Moly Lube - Club Car Part No. 1012151 Quarterly by Owner or Trained Technician Brake Linkage and Pivots Dry Moly Lube - Club Car Part No.
1012151 Accelerator pivots Dry Moly Lube - Club Car Part No. LUBRICATION POINTS POWERDRIVE SYSTEM 48 AND POWERDRIVE PLUS VEHICLES WITH MULTI-STEP POTENTIOMETERS, AND V-GLIDE 36 VOLT VEHICLES DO NOT LUBRICATE FORWARD & REVERSE SWITCH ON POWERDRIVE PLUS VEHICLES FIGURE 4-3 VEHICLE CAPACITIES CAPACITIES GASOLINE VEHICLES ELECTRIC VEHICLES Engine Crankcase without filter 32 oz. PERIODIC SERVICE - GASOLINE VEHICLES WARNING. IF ANY PROBLEMS ARE FOUND DURING SCHEDULED INSPECTION OR SERVICE, DO NOT OPERATE VEHICLE UNTIL REPAIRS ARE MADE. FAILURE TO MAKE NECESSARY REPAIRS COULD RESULT IN FIRE, PROPERTY DAMAGE, SEVERE PERSONAL INJURY, OR DEATH. PERIODIC SERVICE SCHEDULE - GASOLINE VEHICLE REGULAR INTERVAL SERVICE Wash battery top with baking soda/water solution Battery (See Section 22).
Check brake cables for damage; replace as required. Check for proper operation (See Performance Inspec- Brake System tion, Page 3-2 in the Maintenance & Service Manual). Check brake pedal free play. PERIODIC SERVICE SCHEDULE - GASOLINE VEHICLE REGULAR INTERVAL SERVICE Check for proper operation.
Inspect belt and replace Torque Converter/Drive Belt as required (See Section 16). Semi-annual Service by Check for cracks, wear, and glazing, replace if neces- Trained Mechanic Only sary. PERIODIC SERVICE SCHEDULE - ELECTRIC VEHICLES REGULAR INTERVAL SERVICE Batteries Charge batteries. Check for proper operation (See Performance Inspec- Brake System tion, Page 3-2 in the Maintenance & Service Manual). Adjust as necessary. Charger and Receptacle Check for damage and snug fit. Check for proper operation (See Performance Inspec- Park Brake tion, Page 3-2 in the Maintenance &.
SECTION 5 - BODY AND TRIM All information in Section 5 of the 1995 - 1996 DS Maintenance and Service Manual, Club Car Part Number 1019051-01, is current for 1997. However, the following CAUTION, which is not stated in the manual, should also be heeded. SOUNDING, THE CONTROLLER IS DISCHARGED. NOTE.
CONTINUOUSLY VARIABLE POTENTIOMETERS WERE STANDARD ON EARLY 1997 DS POW- ERDRIVE SYSTEM 48 AND POWERDRIVE PLUS VEHICLES. ON DS POWERDRIVE SYSTEM 48 AND POWERDRIVE PLUS VEHICLES SERIAL NO.
9711-564736 AND LATER, THE MULTI-STEP POTENTIOMETER IS STANDARD. PEDAL GROUP ADJUSTMENT 1.
ADJUST BRAKE PEDAL HEIGHT - ALL DS VEHICLES 1.1. To provide slack in the brake cables, loosen hex nuts on the brake equalizer rod (Figure 6-1). AFTER LOOSENING JAM NUT (31) WITH A 7/16' SOCKET, ROTATE PEDAL STOP (22) UPWARD TO DECREASE DISTANCE BETWEEN PEDAL AND.
NOTE. ON ALL 1997 DS GASOLINE VEHICLES AND V-GLIDE 36 VOLT ELECTRIC VEHICLES, AND ON 1997 POWERDRIVE SYSTEM 48 AND POWERDRIVE PLUS VEHICLES SERIAL NO. 9711-564736 AND LATER, THE ACCELERATOR ROD ADJUSTMENT MUST ALSO BE CHECKED IF THE RATCHET/PAWL GAP IS ADJUSTED (SEE STEP 4, PAGE 19, OR STEP 4, PAGE 20). yyyyy yyyyy RATCHET (B) TOOTH LENGTH LOCKED POSITION yyyyy WITH PARK BRAKE UNLOCKED MEASURE FROM FLOOR BOARD TO BACK yyyyy OF ACCELERATOR MAKE SURE PAWL (A) ENGAGES AT LEAST 75% OF RACHET TOOTH LENGTH (B) FIGURE 6-5 FIGURE 6-6 SNAP LOOSE BALL JOINT ( 11) FROM 1/2 INCH WRENCH BEHIND PARK BRAKE PEDAL 1/2 INCH SOCKET.
Adjust the Accelerator Rod - Gasoline Vehicles Only: DANGER. BEFORE SERVICING, TURN THE KEY SWITCH TO OFF AND PLACE THE FORWARD AND REVERSE LEVER IN THE NEUTRAL POSITION. TO PREVENT ACCIDENTAL STARTING OF THE ENGINE, DISCONNECT THE BATTERY CABLES, NEGATIVE (-) FIRST. Adjust the Accelerator Rod, Gasoline Vehicles, Continued: NOTE. AFTER THE PEDAL GROUP AND ACCELERATOR ROD ARE ADJUSTED, THE FINAL GOV- ERNED ENGINE RPM SHOULD BE SET PER SPECIFICATIONS IN SECTION 13, PAGE 13-50.
If the events above occur as they should, hold the ball joint at each end of the accelerator rod with pliers and tighten the accelerator rod jam nut against it. Adjust the Actuator Lever (There is no accelerator rod on PowerDrive System 48 or PowerDrive Plus vehicles prior to serial number 9711-564736): 4.1. Connect the Calibration Test Module (Club Car Part No. 1018871-01) (Figure 6-12, Page 22) to the vehicle. SOCKET TO MOTOR SPEED SENSOR PLUG, ROTATE MOTOR.
SHOULD PULSE ON AND OFF INDICATING SPEED SENSOR IS FUNCTIONAL. BUTTON SEE OPERATING INSTRUCTIONS FOR MORE DETAIL POWER MODE Club Car SSAM FIGURE 6-12 FIGURE 6-13 4 5/8' 3/32' READS MICRO. With the actuator in this position, tighten the actuator bolt slightly.
Using a 5/16” wrench, loosen the potentiometer adjustment lock nut (See Figure 6-17). Using a potentiometer adjustment tool or very small flat blade screwdriver (electronics type), turn the potentiometer adjustment screw until the test module reads from 3.38 to 3.42 volts. Adjusting Actuator Lever on PowerDrive System 48 and PowerDrive Plus Vehicles, Continued: 4.12. Check potentiometer adjustment (See 1995-1996 DS Maintenance and Service Manual, Sec- tion 20A, Page 20-17).
Install the potentiometer housing cover. NOTE. THE POTENTIOMETER IS PRESET AT THE FACTORY AND SHOULD NOT REQUIRE ADJUST- MENT. PEDAL GROUP DISASSEMBLY AND ASSEMBLY ALL VEHICLES Removing the Brake Pedal Assembly 1. Make sure key switch is off and that the Forward and Reverse Switch is in neutral, then disconnect bat- tery or batteries as shown (In the Maintenance and Service Manual, see Figure 12-1, Page 12-2 for gasoline vehicles, or Figure 22-5 or 22-6, Page 22-5 for electric vehicles).
FIGURE 6-20 1.4. Install the brake cables (14) on the equalizer rod using new cotter pins (16) and the clevis pins (17) that were removed when the brake pedal assembly was disassembled (Figure 6-20). Tighten the nut (24) on the equalizer rod so that brake pedal free-play is 1/4 inch to 1/2 inch (6.35 mm to 12.7 mm) (Figure 6-24, Page 28).
Place chocks under the rear wheels and lift the front end of the vehicle with a chain hoist or floor jack. Place jackstands under the front cross tube of the vehicle frame and lower the vehicle onto the jack- stands. REMOVING THE ACCELERATOR PEDAL ASSEMBLY PowerDrive System 48 and PowerDrive Plus Electric Vehicles Serial Number 9711- 564736 and Later, and all 1997 DS V-Glide 36 Volt and DS Gasoline Vehicles. (For PowerDrive System 48 and PowerDrive Plus vehicles prior to serial number 9711-564736, see page 30). PowerDrive System 48 and PowerDrive Plus Electric Vehicles Serial Number 9711- 564736 and Later, and all 1997 DS V-Glide 36 Volt and DS Gasoline Vehicles. Position the accelerator pivot rod supports (23) on the vehicle frame and install the four bolts (24), flat washers (8), and lock nuts (16). Pedal Group Disassembly and Assembly, Continued: 8.
Rotate the ratchet clockwise until it touches the park brake pawl, then slide the ratchet onto the splines of the pivot rod (it may be necessary to push the pivot rod toward the driver side of the vehicle to make the splines accessible). Remove the two hex head screws (20) attaching the potentiometer housing cover (Figure 6-15, Page 23) to the potentiometer and remove the cover. Remove the bolt (9), washer (8) (See NOTE below), and lock nut (11) from the spring retainer (12) with the pivot support bearing (10) (Figure 6-19, Page 24). Pedal Group Disassembly and Assembly, Continued: 4.
Rotate the potentiometer lever (27) clockwise until lever fork is at the two o’clock position (Figure 6-25). The lever must be at approximately two o’clock in order for it to mate with the alignment pin on the actu- ator lever. Install the nut (24) (Figure 6-19, Page 24) on the accelerator pivot rod and tighten it to 16-20 ft.lbs. (22/ 27 N-m). See NOTE below.
NOTE. MAKE SURE THE ACTUATOR LEVER AND THE POTENTIOMETER LEVER ARE STILL MATED BEFORE TIGHTENING THE ACCELERATOR PIVOT ROD RETAINING NUT.
See Section 10 of the 1995 - 1996 Maintenance and Service Manual, Club Car Part Number 1019051-01. Because of incorporation of the unitized transaxle in 1997 DS gasoline vehicles, Section 10 in the 1995-1996 DS Maintenance and Service Manual becomes Section 9 in this supplement. SECTION SECTION 10 - UNITIZED TRANSAXLE This section supersedes Sections 9 and 17 in the 1995-1996 DS Maintenance and Service Manual. GENERAL INFORMATION All 1997 model gasoline powered DS Golf Cars are equipped with heavy-duty, fully-synchronized Unitized Transaxles.
The unitized transaxle replaces the transmission / transaxle combination that was used previ- ously, and performs the functions of both. 7/16” Socket, 3/8 Drive Small Flat Blade Screwdriver Feeler Gauge 1/2” Socket, 3/8 Drive Medium Flat Blade Screwdrivers (2) Seal Puller (Club Car Part No. 1012809) 9/16” Socket, 3/8 Drive Small Phillips Head Screwdriver 16” Rolling Wedge Bar 5/8” Socket, 3/8 Drive 1/4”. 12” to 18” Straight Edge 7/16” Open End Wrench Small Knife or Wire Snippers Bearing Puller Wedge Attachment (Club Car Axle Seal Tool (Club Car Part No.
Governor Gear Shaft Installation Tool Part No. 1012812) 1014162) (Club Car Part No. 1019331-01) UNITIZED TRANSAXLE LUBRICATION There are two plugs located on the right (driven clutch) side of the unitized transaxle (Figure 10-2). Inspect the bearing. If the bearing is damaged or worn, replace it.
AXLE BEARING Removing the Axle Bearing 1. Remove the retaining ring (74), then place a bearing puller wedge attachment (Club Car Part No. 1012812) on the axle shaft between the wheel mounting flange and the bearing. CAUTION. APPLY LOCTITE 271 TO THE INSIDE OF THE COLLAR ONLY, NOT TO THE SHAFT - SO THAT THE LOCTITE WILL BE PUSHED AWAY FROM THE BEARING AS THE COLLAR AND BEARING ARE PRESSED ON.
IF LOCTITE GETS ON OR IN THE BEARING, THE BEARING MUST BE REPLACED. Place a new seal (72) (Figure 10-6) in the axle tube with seal lip facing away from the bearing.
Use an axle seal tool (Club Car Part No. 1014162) to press it in until it seats firmly in position (Figure 10-8). LOOSEN TUBE RETAINER, THEN PULL FUEL OVERFLOW TUBE FROM CARBURETOR FIGURE 10-9 FIGURE 10-10 REMOVING THE UNITIZED TRANSAXLE WARNING.
TO AVOID UNINTENTIONAL STARTING OF THE VEHICLE, ALWAYS BEFORE SERVICING: - DISCONNECT THE BATTERY CABLES, NEGATIVE FIRST. DISCONNECT THE SPARK PLUG WIRE FROM THE SPARK PLUG. Removing the Unitized Transaxle, Continued: TOP VIEW LOOSEN RETAINING NUTS REMOVE FUEL LINE TO REMOVE THROTTLE USING A 1/4' NUT DRIVE CABLE FROM ELECTRIC BOX OR FLAT BLADE SCREWDRIVER FIGURE 10-13 FIGURE 10-14 2.4. Use a 1/4” nut driver to loosen the hose clamp and then disconnect the fuel line from the carbure- tor (Figure 10-13). REMOVE GROUND REMOVE YELLOW WIRE WIRE AT A2 TERMINAL PULL OIL SENDING UNIT REMOVE WIRE FROM ENGINE WHITE WIRE MARK WIRES FOR PROPER RECONNECTION FIGURE 10-17 FIGURE 10-18 UNPLUG IGNITION KILL WIRE WHITE/BLACK WIRE BLACK WIRE FIGURE 10-19 FIGURE 10-20 3. Removing the Transaxle, Continued: POSITION FLOORJACK UNDER BUMPER SUPPORT DISCONNECT SHOCK ABSORBERS FROM LOWER MOUNTS FIGURE 10-21 FIGURE 10-22 8. Continue raising the vehicle until the rear bumper is higher than the top of the unitized transmission (high enough to allow the transaxle and engine to be rolled under it and out of the vehicle) (Figure 10- 25).
RAISE REAR OF VEHICLE UNTIL DRIVE TRAIN CAN BE ROLLED OUT JACKSTAND WITH JACKSTANDS IN PLACE, REMOVE JACKSTAND FLOORJACK FIGURE 10-25 FIGURE 10-26 SNUBBER BRACKET LOWER SNUBBER TO THE GROUND VEHICLE BODY AND FRAME REMAIN STATIONARY ON LIFT SNUBBER JACKSTANDS WHILE OUT OF BRACKET ROLL ENTIRE DRIVETRAIN IS ROLLED. Removing the Transaxle, Continued: USING WOODEN BLOCKS, GRASP BELT MIDWAY PROP ENGINE PAN UP SO BETWEEN DRIVE AND THAT IT IS LEVEL WITH FLOOR DRIVEN CLUTCHES, THEN ROLL BELT OFF DRIVEN CLUTCH ENGINE DRIVEN CLUTCH APROX. 6' DRIVE CLUTCH FIGURE 10-29 FIGURE 10-30 16. USE A 3/8' SOCKET OR WRENCH TO REMOVE TWO SCREWS HOLDING ACCELERATOR CABLE RETAINING BRACKET BRACKET USE A 3/8' WRENCH OR SOCKET TO REMOVE TWO SCREWS HOLDING GOVER- NOR CABLE BRACKET FIGURE 10-33 FIGURE 10-34 TRANSAXLE MOUNTING BOLT AND NUT (TYPICAL 4 PLACES) WOODEN BLOCKS. Unitized Transaxle Disassembly, Continued: NOTE. TO SEPARATE THE SECTIONS, IT MAY BE NECESSARY TO TAP LIGHTLY WITH A RUBBER MALLET ON THE SPLINE OF THE INPUT PINION. FIGURE 10-36 Page 48.
Remove the synchronizer gear assembly and shift fork assembly as a unit from the casing (Figure 10- 39, Page 50). Use a seal puller (Club Car Part No. 1012809) or rolling wedge bar to remove the input shaft oil seal from the casing (Figure 10-40, Page 50). Unitized Transaxle Disassembly, Continued: 15.2. Remove the pivot arm by pulling it through the wall to the interior of the casing. Use a small chisel or similar pointed instrument to pry the pivot arm oil seal (22) (Figure 10-36, Page 48) out of the casing (See Figure 10-42). Remove the differential gear (91) from the carrier case (Figure 10-6, Page 39).
If the bearings (79) are to be removed, place a bearing puller wedge attachment (Club Car Part No. 1012812) between the bearing and carrier casing (84) and press the bearing off as shown (Figure 10- 48, Page 55).
SEMBLED IN THEIR ORIGINAL LOCATIONS AND ORIENTATIONS. Place a bearing puller wedge attachment (Club Car Part No. 1012812) between the bearing (38) and spur (governor drive) gear (40) (Figure 10-43, Page 53), then press the bearing off the input shaft as shown (Figure 10-49, Page 9-55).
REFERENCE DRIVER SIDE CASE REFERENCE PASSENGER SIDE CASE FIGURE 10-43 2. Place the bearing puller wedge attachment under the bearing (59) and press the bearing from the shaft (Figure 10-43). See CAUTION at bottom of page 52. Press the gear (58) from the shaft (56), then remove the key (57) (Figure 10-43). DISASSEMBLE THE IDLER SHAFT ASSEMBLY 1.
Place a bearing puller wedge attachment (Club Car Part No. 1012812) between the bearing (66) (Fig- ure 10-43, Page 53) and the small gear on the idler shaft, then press the bearing off the shaft as shown (Figure 10-52, Page 56).
X is.020 inch (0.51 millimeter) or less (Figure 10-55, Page 57). USE A 1-3/8' O.D. PRESS ARBOR AND A BEARING PULLER WEDGE ATTACHMENT (CLUB CAR #1012812) ARBOR TO PRESS BEARING FROM GEAR CASE WEDGE ATTACHMENT. (CLUB CAR #1012812) A 3/4' O.D. OR LESS ARBOR ARBOR TO PRESS BEARING ARBOR AND A FROM SHAFT WEDGE ATTACHMENT (CLUB CAR # 1012812) WEDGE ATTACHMENT FIGURE 10-51 FIGURE 10-52 PRESS RAM PRESS IDLER SHAFT FROM BEARING USING A 3/4' OR LESS O.D. PRESS BEARING ONTO IDLER SHAFT SYNCHRO RING MUST BE REPLACED WHEN (X) DISTANCE IS LESS THAN.020 IN (0.51 MM) TURN IDLER SHAFT OVER AND PRESS BEARING ON OTHER END FIGURE 10-55 FIGURE 10-56 PRESS TOP OF SPLINE INSTALL SNAP RINGS ON BOTH SIDES OF SYNCHRONIZER MACHINED. Synchronizer Gear Assembly, Continued: 6.
Install the thrust washer (41) and two bearings (43) as shown (Figure 10-43, Page 53). Install the input gear assembly (52), with the smooth collar toward the synchronizer ring as shown (Fig- ure 10-43).
The input gear should seat in the synchronizer ring. Install thrust plate (41) onto the shaft, and the dowel pin (50) into the shaft as shown (Figure 10-43). Install the spur (governor drive) gear (40) onto the shaft with either side down. Mate the notch in the gear with the dowel pin as shown (Figure 10-43, Page 53). Differential Gear Case Assembly, Continued: POSITION POSITION SECOND DIFFERENTIAL THRUST PLATE AND GEAR AND SECOND IDLER GEAR THRUST PLATE IN DIFFERENTIAL IN CARRIER GEAR CARRIER CASE COVER.
CASE.THEN CONTINUE TAPPING PIN THROUGH SECOND IDLER GEAR AND THRUST PLATE UNTIL PIN IS FLUSH WITH OUTSIDE OF HOUSING.THEN, WHILE. FIGURE 10-67 3. Position the governor gear shaft installation tool (Club Car Part No. 1019331-01) over the shaft bore in the inside of the left (driver) side casing and insert the governor gear shaft into the tool, long end (from the groove) first, as shown (Figure 10-69, Page 62). Unitized Transaxle Assembly, Continued: INSTALL SHIFTER SHAFT AND GOVERNOR SHAFT SEALS POSITION THE GOVERNOR INTO THEIR SEATS GEAR SHAFT TOOL SHAFT OVER THE SHAFT BORE IN THE CASING, THEN INSERT LONG END OF THE GOVERNOR GEAR SHAFT THROUGH TOOL AND INTO BORE. TOOL.TAP GOVERNOR GEAR SHAFT THROUGH THE. they are seated.
When all of the assemblies are correctly seated, the outside edges of the input drive gear (52) and the intermediate gear (58) (See Figure 10-43, Page 53) should be flush (in the same plane) as shown (Figure 10-80, Page 65). Also, the outside surfaces of the idler gear bearing, the intermediate gear bearing, and the differential gear bearing should be flush (Figure 10-80, Page 65). Unitized Transaxle Assembly, Continued: INSTALL DIFFERENTIAL GEAR ASSEMBLY INTO INSERT THE IDLER GEAR BORE IN THE LEFT ASSEMBLY INTO CASING BORE SIDE CASE (GEARS DO NOT MESH) FIGURE 10-74 FIGURE 10-75 POSITION SHIFTER PLACE A DROP OF CYANOACRYLATE ADHESIVE FORK ON SYNCHRONIZER SLEEVE. SEVERAL GEARS MESH AS YOU INSERT THE SYNCHRONIZER GEAR AS YOU INSERT THE ASSEMBLY (COMPLETE WITH SHIFTER FORK) INTERMEDIATE INTO THE CASING, SEVERAL GEARS GEAR ASSEMBLY.
MUST MESH TOGETHER. SPUR GEAR AND GOVERNOR GEAR MESH LARGE IDLER GEAR AND THE SMALL GEAR ON THE SHIFTER SYNCHRONIZER INTERMEDIATE GEAR. Unitized Transaxle Assembly, Continued: 11.3. Duplicate step 11.2 for the left side axle tube. Install the right axle shaft (68) in the right axle tube (76) (Figure 10-6, Page 39).
Using snap ring pliers, install the retaining ring as shown (Figure 10-85). See WARNING below. UNITIZED TRANSAXLE INSTALLATION 1. Install the brake assemblies, wheels, and leaf springs on the transaxle. Position the transaxle mounting plate on the two mounting studs at the rear of the engine, and then install the two mounting nuts (Figure 10-86).
Use a 14 mm wrench. Unitized Transaxle Installation, Continued: ROLL POWERTRAIN UNDER VEHICLE, THEN INSTALL KEY ONTO INPUT SHAFT LIFT SNUBBER INTO THE SNUBBER BRACKET INSTALL DRIVEN CLUTCH, SNUBBER WASHER (YELLOW SIDE OUT) AND RETAINING BOLT.
TIGHTEN BOLT TO 12-14 FT.LBS. SNUBBER BRACKET FIGURE 10-90 FIGURE 10-91 12. CONNECT IGNITION KILL WIRE WHITE/BLACK WIRE CONNECT SHOCK BLACK ABSORBERS TO WIRE LOWER MOUNTS FIGURE 10-94 FIGURE 10-95 CONNECT GROUND CONNECT YELLOW WIRE WIRE AT A2 TERMINAL CONNECT OIL SENDING CONNECT UNIT WIRE WHITE WIRE FIGURE 10-96 FIGURE 10-97 17.
Connect the engine kill switch wire (18 gauge white/black stripe) to the bullet connector at the lower right front of the engine (Figure 10-95). Unitized Transaxle Installation, Continued: 27. Install the drain plug and tighten to 21 ft.lbs. Fill transaxle with 27 oz. (.8 liter) of 80-90 WT. API Class GL3 or 80-90 WT. AGMA Class EP gear lube.
Install and tighten the level indicator hole plug to 21 ft.lbs. CONNECT TUBE TO CARBURETOR. SQUEEZE CLAMP TO POSITION IT. FIGURE 10-104 FORWARD AND REVERSE SHIFTER CABLE If the forward and reverse shifter cable is jammed or is damaged in any way, it must be replaced. WARNING. WHEN MAKING TESTS OR REPAIRS, ALWAYS: - WEAR SAFETY GLASSES OR APPROVED EYE PROTECTION.
Removal of the Forward and Reverse Shifter Cable, Continued: 2. Remove the ball joint socket (20) from the shifter arm ball stud (19) on the transaxle (Figure 10-107). Loosen the retaining nuts (22) on both ends of the cable (Figure 10-107). Secure the cable with retaining nut (22) and washer (23) on each side of the shifter cable support bracket at the forward and reverse assembly (Figure 10-107). Install the ball joint socket (20) on the shifter lever ball stud (19) on the transaxle (Figure 10-107).
SECTION 11 - TROUBLESHOOTING THE GASOLINE VEHICLE Your Club Car DS vehicle will operate for a longer period of time without repairs if it is given proper care and preventive maintenance. The following check list will be helpful in identifying operating difficulties should they occur. SYMPTOM POSSIBLE CAUSES REFER TO Engine does not start Igniter failed Section 12 - Gasoline Vehicle Electrical easily, continued: System Low cylinder compression Section 13 - Engine Water or dirt in the fuel Section 14 - Fuel System system and/or carburetor; dirty or clogged fuel filter Carburetor improperly Section 14 - Fuel System. SYMPTOM POSSIBLE CAUSES REFER TO Loss of engine power.
Exhaust valve is restricted with carbon Section 13 - Engine deposit Muffler or exhaust pipe restricted with Section 15 - Exhaust System carbon or other substance Igniter failed Section 12 - Gasoline Vehicle Electrical System Air filter is dirty or clogged Section 14 - Fuel System. SYMPTOM POSSIBLE CAUSES REFER TO Starter fails to operate, continued: Starter solenoid failed Section 12 - Gasoline Vehicle Electrical System - Starter circuit Accelerator limit switch failed Section 12 - Gasoline Vehicle Electrical System - Starter circuit Key switch failed Section 12 - Gasoline Vehicle Electrical System - Starter circuit. SYMPTOM POSSIBLE CAUSES REFER TO Damaged driven clutch Section 16 - Torque Converter Excessive vehicle Damaged starter/generator pulley Section 12 - Gasoline Vehicle vibration, continued: Electrical System - Starter/Generator Misaligned clutches Section 16 - Torque Converter RPM setting is incorrect Section 14 - Fuel System Drive belt is worn, cracked, glazed, or Section 16 - Torque Converter. SECTION SECTION 12 - ELECTRICAL SYSTEM GASOLINE VEHICLES This section supersedes Section 12 in the 1995-1996 DS Maintenance and Service Manual. DANGER. GASOLINE VAPORS - FLAMMABLE - DO NOT SMOKE!
KEEP SPARKS, FLAMES, CIGA- RETTES AWAY. TOOLS, WIRES AND METAL OBJECTS CAN CAUSE SPARKS WHEN “SHORTED”. Electrical System - Gasoline Vehicles, Continued: CAUTION. BEFORE REMOVAL AND DISASSEMBLY, CLEAN THE ENGINE. ANY DIRT ENTERING THE ENGINE, CARBURETOR, OR OTHER PARTS WILL WORK AS AN ABRASIVE AND SHORTEN THE LIFE OF THE ENGINE. FOR THE SAME REASON, BEFORE INSTALLING A NEW PART, CLEAN OFF ANY DUST OR METAL FILINGS. The starter circuit consists of a twelve-volt battery, fuse, key switch, accelerator starter limit switch, neutral lock-out limit switch, solenoid, starter, and connecting wires.
The battery is the source of power for the system. The fuse provides protection to the solenoid activating cir- cuit. FIGURE 12-3 THE GENERATOR CIRCUIT (FIGURE 12-4) The generator circuit consists of the starter/generator, voltage regulator, solenoid, the battery, and connect- ing wires. When battery power is first supplied to the starter/generator, the starter/generator turns the engine at low RPM (approx. Once the engine starts running, it then drives the starter/generator. At any engine RPM over 1215 (3000 starter/generator RPM), the starter/generator functions as a generator, supplying charging current to the battery. SPARK PLUG RPM LIMITER IGNITION COIL WITH IGNITER ENGINE KILL WIRE BULLET CONNECTOR FIGURE 12-5 ENGINE KILL CIRCUIT (FIGURE 12-6) The exciter coil in the ignition coil supplies electrical power for the spark plug, therefore the proper way to stop the engine is to run this electrical power to ground, by-passing the spark plug.
The engine kill circuit consists of the key switch, a kill limit switch that is activated by the accelerator pedal, a neutral lock-out limit switch that is activated by a cam located on the back of the forward and reverse assem- bly, and connecting wires. LOW OIL WARNING CIRCUIT (FIGURE 12-8) (M-) KEY SWITCH FIGURE 12-7 FIGURE 12-8 The low oil warning circuit consists of an oil sending unit in the engine, a dash mounted oil light, and connect- ing wires.
The light picks up power from the key switch when the key switch is turned to the ON position. When the oil level in the crankcase is low, the oil sending unit closes the circuit to the ground and illuminates the oil light. NEUTRAL FORWARD FORWARD NEUTRAL SERVICE POSITION OPERATE POSITION FIGURE 12-10 FIGURE 12-11 CIRCUIT TESTING DANGER. DO NOT OPERATE GASOLINE VEHICLE IN AN ENCLOSED AREA WITHOUT PROPER VENTI- LATION. ENGINE PRODUCES CARBON MONOXIDE WHICH IS AN ODORLESS, DEADLY POI- SON. Testing the Vehicle Battery, Continued: 4. Place the red (+) probe of a multimeter, set at Volts - DC, 20 volt range, on the positive (+) post and place the black (-) probe on the negative (-) post of the battery and take a voltage reading.
If it shows less than 12.4 volts, or if the lowest specific gravity reading from Step 3 is less than 1.225, recharge the battery. DANGER. DO NOT OPERATE GASOLINE VEHICLE IN AN ENCLOSED AREA WITHOUT PROPER VENTI- LATION.
ENGINE PRODUCES CARBON MONOXIDE WHICH IS AN ODORLESS, DEADLY POI- SON. WARNING.
WHEN MAKING ELECTRICAL TESTS OR REPAIRS, ALWAYS: - WEAR SAFETY GLASSES OR APPROVED EYE PROTECTION. REMOVE THE KEY. Circuit Testing, Continued: DANGER. DO NOT OPERATE GASOLINE VEHICLE IN AN ENCLOSED AREA WITHOUT PROPER VENTI- LATION.
ENGINE PRODUCES CARBON MONOXIDE WHICH IS AN ODORLESS, DEADLY POI- SON. WARNING. WHEN MAKING ELECTRICAL TESTS OR REPAIRS, ALWAYS: - WEAR SAFETY GLASSES OR APPROVED EYE PROTECTION. REMOVE THE KEY. ENGINE WILL NOT STOP RUNNING WHEN KEY SWITCH IS IN OFF POSITION CHECK KEY SWITCH (TEST PROCEDURE 16) INCORRECT CORRECT CONTINUITY READING CONTINUITY READING REPLACE KEY SWITCH CHECK CONNECTIONS OF CIRCUIT WIRING WIRES INCORRECTLY WIRES CORRECTLY CONNECTED CONNECTED CONNECT WIRES CORRECTLY CHECK CONTINUITY OF CIRCUIT WIRES (TEST PROCEDURE 8). DANGER. DO NOT OPERATE GASOLINE VEHICLE IN AN ENCLOSED AREA WITHOUT PROPER VENTI- LATION.
ENGINE PRODUCES CARBON MONOXIDE WHICH IS AN ODORLESS, DEADLY POI- SON. WARNING. WHEN MAKING ELECTRICAL TESTS OR REPAIRS, ALWAYS: - WEAR SAFETY GLASSES OR APPROVED EYE PROTECTION. REMOVE THE KEY. TESTING THE LOW OIL WARNING CIRCUIT Use the chart below (Figure 12-17) as a starting point for troubleshooting the low oil warning circuit.
OIL LIGHT WILL NOT ILLUMINATE WHEN ENGINE OIL IS LOW CHECK WIRE CONNECTION TO THE OIL SENDING UNIT (TEST PROCEDURE 20) WIRES INCORRECTLY WIRES CORRECTLY. Circuit Testing, Continued: WARNING. WHEN MAKING ELECTRICAL TESTS OR REPAIRS, ALWAYS: - WEAR SAFETY GLASSES OR APPROVED EYE PROTECTION. REMOVE THE KEY. PUT THE FORWARD AND REVERSE SWITCH IN NEUTRAL. DISCONNECT THE BATTERY AS SHOWN (FIGURE 12-1, PAGE 82).

Check that the wires are connected correctly and are tight. If they are not, rewire or tighten as neces- sary.
Remove the fuse. Using a multimeter set on ohms (Ω), place the red (+) probe on one terminal of the fuse and place the black (-) probe on the other terminal of the fuse. Test Procedure 3 - Ground Straps, Continued: YELLOW BLUE DATA HOLD AC/DC 500V MAX 250V MAX AC V DC V DATA HOLD WHITE / AC/DC 500V MAX 250V MAX WHITE BLACK AC V DC V PLACE BLACK (-) PROBE ON FRAME DISCONNECT THE 6 GAUGE BLACK WIRE KEY SWITCH FROM THE BATTERY.
lever in NEUTRAL, and the accelerator pedal in the UP position, the reading should be no continuity. With the accelerator pedal depressed, the reading should be continuity. If readings are incorrect, replace the switch. Test Procedure 5 - Solenoid: 1. Place the neutral lock-out cam in the SERVICE position, put the forward and reverse lever in the NEU- TRAL position, and chock the wheels.
SOLENOID SOLENOID DATA HOLD AC/DC 500V MAX 250V MAX DATA HOLD AC V AC/DC 500V MAX DC V 250V MAX AC V DC V ELECTRICAL COMPONENT ELECTRICAL COMPONENT BOX FRAME FIGURE 12-22 FIGURE 12-23 Test Procedure 6 - Cam-Activated Neutral Lock-out Limit Switch: This switch is located on the forward and reverse switch assembly. Check for proper wiring and tight connections. Place the red (+) probe of the multimeter on the common (COM) terminal of the limit switch. Place the black (-) probe on the normally open (NO) terminal of the limit switch. Without the lever depressed, the reading should be no continuity.
Test Procedure 7, Continued: 6. Disconnect the yellow wire from the DF terminal and the green wire from the F1 terminal on the starter/ generator. Using a multimeter set on ohms (Ω), place the red (+) probe on the DF terminal and the black (-) probe on the F1 terminal.
Test Procedure 10 - Voltage Regulator: DANGER. DO NOT OPERATE GASOLINE VEHICLE IN AN ENCLOSED AREA WITHOUT PROPER VENTI- LATION. ENGINE PRODUCES CARBON MONOXIDE WHICH IS AN ODORLESS, DEADLY POI- SON.
NOTE. LEAVE THE BATTERY CONNECTED WHILE PERFORMING TEST PROCEDURE 10. Test Procedure 11 - Ignition Spark, Continued: 2.
Remove the plug wire from the spark plug. Using an ignition spark gap test tool (Thexton 404® or equivalent), check for correct spark (Figure 12-28, Page 101). Adjust the tester probes to approximately 18,000 volts (18 Kv) setting.
Connect the tester to the spark plug wire, and connect the alligator clip to the frame. WARNING.
WHEN MAKING ELECTRICAL TESTS OR REPAIRS, ALWAYS: - WEAR SAFETY GLASSES OR APPROVED EYE PROTECTION. REMOVE THE KEY. PUT THE FORWARD AND REVERSE SWITCH IN NEUTRAL. DISCONNECT THE BATTERY AS SHOWN (FIGURE 12-1, PAGE 82). Test Procedure 14 - Disconnected Kill Wire, Continued: 3.
Disconnect engine-kill white/black wire at bullet connector located by the RPM limiter (Figure 12-32). With the neutral lock-out cam placed in the SERVICE position and the wheels chocked, connect the 6 gauge red wire to the positive post on the battery, then connect the 6 gauge black wire to the negative post. on the (M-) terminal. With the key switch turned OFF, the reading should be continuity.
With the key switch turned ON, the reading should be no continuity. If either reading is incorrect, replace the key switch. Test Procedure 17 - Fuse: The fuse (red 10 amp) is located in the electrical component box (See Removing the Fuse, Page 120). Test Procedure 21 - Oil Warning Light, Continued: 3.
Check that the wires are connected correctly and are tight. If they are not, rewire or tighten as neces- sary (Figure 12-8, Page 86). Disconnect the yellow wire (to the oil sending unit) from the terminal on the oil light. Using an alligator clip jumper wire, connect the terminal to the frame of the vehicle. Turn the key switch to the ON position, leave the forward and reverse switch in the neutral position and depress the accelerator pedal (with the accelerator pedal depressed the battery is under load). If the voltage reading is over 8 volts, check the starter/generator (See Starter/Generator below, Pages 107- 116). Disassembly of the Starter/Generator to Service the Brushes 1.
Remove the two bolts (20) and washers (21 and 22) and pull commutator end cover (23) free of starter housing (24) (Figure 12-37). See NOTE below. NOTE. IF THE BRUSHES ARE NOT REMOVED, CONTACT BETWEEN THE BRUSHES AND COMMUTA- TOR AS THE COMMUTATOR END COVER IS BEING REMOVED OR INSTALLED COULD POSSI- BLY DAMAGE THE BRUSHES.
Cleaning, Inspection, and Replacement of Brush Springs CAUTION. WHEN CHECKING BRUSH SPRING TENSION, DO NOT PUSH SPRINGS BEYOND THE POINT THEY WOULD NORMALLY BE IF THERE WERE NEW BRUSHES INSTALLED. EXERTING EXCES- SIVE FORCE OR PUSHING BRUSH SPRINGS BEYOND THEIR NORMAL RESTING POINT WILL DAMAGE SPRINGS. Assembly of the Starter/Generator, Continued: 3. Install the commutator end cover (23) onto the armature shaft.
Align the locating pin with the pin hole in the cover. Install the two M6 x 180mm screws (20) and tighten to 95-104 in.lbs. (10.6/11.6 N-m) (Fig- ure 12-37, Page 108). Disassembly of the Starter/Generator to Service Armature/Commutator, Continued: 2. To separate armature (33) from output end cover (36), remove nut (41), lockwasher (40), pulley (39), shaft key (34), spacer (37), and bearing retainer screws (43) (Figure 12-42). Clean and Inspect the Bearings 1. Make sure the wedge attachment tool is supporting the inner race of the bearing but is not contacting the armature shaft.
If a press is not available, secure a bearing puller (Club Car Part No. 1012811) to the wedge attachment tool and pull the bearing off of the end of the armature shaft.
Support the arma- ture so that it will not drop when the bearing is removed (Figure 12-44). Flared armature windings. Worn, burned, or glazed commutator. Loose or raised commutator bars. Bruised or damaged armature core laminations. Worn armature bearing or shaft. Dirty or oily commutator.
POLE PIECE SCREW RETAINING NUT POLE PIECE INSULATOR HOUSING FIELD COIL. Cleaning, Inspection, and Replacement of the Commutator, Continued: CAUTION. NEVER USE EMERY CLOTH ON THE COMMUTATOR.
PARTICLES OF EMERY ARE CONDUC- TIVE AND MAY SHORT-CIRCUIT THE COMMUTATOR BARS. NEVER USE OIL OR LUBRICANTS ON THE COMMUTATOR OR BRUSHES. Using a micrometer, measure the outside diameter at two points along the commutator. If the commu- tator outside diameter is less than 1.535 inches (39 millimeters), replace the armature and bearings (Figure 12-46, Page 113).
Assembly of the Starter/Generator 1. Place the field coil inside of the housing. The two insulators that look the same fit into the slots next to the F1 and F2 markings on the outside of the housing. The insulator that looks different slides into the slot next to the DF marking. Starter/Generator Assembly, Continued: 5. Slide the housing with field coils over the armature.
Use the locating pin to align housing to the cover. NOTE.
THE TERMINAL INSULATORS SHOULD BE ON THE COMMUTATOR END OF THE HOUSING. To prevent contact between brushes and commutator as the commutator cover is installed, and possi- ble damage to the brushes, lift the brush springs out of the notches in the brushes and pull the brushes back from the center of the commutator end cover. (3) around the pulley (10) on the end of the starter/generator (1). Place the ten- sion tool (13) (Club Car Part No. 1016867) between the starter/generator and the starter/generator mounting bracket (2) so that the tension tool will lift up the starter/generator. Belt Tension Adjustment, Continued: NOTE.
IF A BURROUGHS GAUGE IS USED, TENSION SHOULD BE ADJUSTED TO 120 LBS. FOR A NEW BELT OR 80-100 LBS FOR A PREVIOUSLY USED BELT. Reinstall the access panel (Figure 12-35, Page 106). VOLTAGE REGULATOR Removing the Voltage Regulator (Figure 12-49) WARNING. Reconnect wires to key switch (See Figure 12-2, Page 83).
1991 Club Car Golf Cart Service Manual Pdf
Coat the connectors with Battery Protector Spray (Club Car Part No. 1014305) to ward off corrosion.
Reverse removal procedures to install key switch in the dash. Be sure that key switch terminals cannot touch the frame and that panel is properly seated and snapped in place. Removing the Solenoid, Continued: WARNING. WHEN MAKING ELECTRICAL TESTS OR REPAIRS, ALWAYS: - WEAR SAFETY GLASSES OR APPROVED EYE PROTECTION. REMOVE THE KEY. PUT THE FORWARD AND REVERSE SWITCH IN NEUTRAL. DISCONNECT THE BATTERY AS SHOWN (FIGURE 12-1, PAGE 82).
ACCELERATOR STARTER LIMIT SWITCH Removing the Accelerator Starter Limit Switch (Figure 12-50) 1. Remove seat from body. Disconnect battery wires as shown (Figure 12-1, Page 82). Remove electrical component box cover (1). Disconnect the green wire and the orange wire from the accelerator starter limit switch (11). Removing the Kill Limit Switch, Continued: WARNING.
WHEN MAKING ELECTRICAL TESTS OR REPAIRS, ALWAYS: - WEAR SAFETY GLASSES OR APPROVED EYE PROTECTION. REMOVE THE KEY.
PUT THE FORWARD AND REVERSE SWITCH IN NEUTRAL. DISCONNECT THE BATTERY AS SHOWN (FIGURE 12-1, PAGE 82). WARNING. DO NOT OVER-TIGHTEN THE RETAINING NUTS. IF THE NUTS ARE OVER-TORQUED, LIMIT SWITCHES COULD BE DAMAGED. Connect the black wire to common (COM) terminal, the green wire to the normally open (NO) terminal and the white wire to the normally closed (NC) terminal of the neutral lock-out limit switch. Removing the Neutral Lock-out Cam, Continued: 3.
Remove the external snap ring (14). Remove the plastic washer (12) and the spring (13). Remove the cam (11). Installing the Neutral Lock-out Cam (Figure 12-52): 1.
Install the cam (11). Disconnect the battery wires as shown (Figure 12-1, Page 82). Disconnect the orange and red/white wires from the reverse buzzer limit switch (4) located on the back of the forward and reverse assembly. Remove the two nuts (2) and washers (6) from the neutral lock-out limit switch (5) and slide the neutral lock-out limit switch off the screws. SEE THE SAFETY WARNINGS ON PAGE 81. General Information 1.
The DS gasoline vehicle is equipped with a 12-volt, low maintenance battery. When replacing the bat- tery in a Club Car gasoline-powered vehicle, the new battery must be the same size as the original. Club Car recommends a group 70, side-post battery (Club Car Part No. 1012328), with a 460 cold- cranking amp rating and a reserve capacity of 85 minutes. The group 70 classification indicates battery size (8 1/4 inches W x 6 1/2 inches D x 7 1/4 inches H). It is important to use the proper size to ensure that the battery hold-down will fit correctly and will properly secure the battery in the vehicle frame. Inspect the hold-down bracket for rust, corrosion or damage.
If both ends of the bracket cannot be fastened securely to the main frame, replace it with a new stainless steel battery hold-down, (Club Car Part No. 1013882), stainless steel flat washers (Club Car Part No. 1011964), and stainless steel nylon insert locknuts (Club Car Part No. Remove the vent cap.
Using a battery thermometer (Club Car Part No.1011767), record the electrolyte temperature of one of the center cells. Squeeze the rubber bulb of the hydrometer and insert into the cell. Slowly release the bulb, drawing electrolyte up into the glass tube of the hydrometer. Hydrometer Calibration, Continued: Most hydrometers are calibrated to read correctly at 80°F. The readings obtained as described above must be corrected for temperature. For each 10°F above 80°F, add.004 to the reading. For each 10°F below 80°F, subtract.004 from the reading.
Interpreting Results of the Hydrometer Test The approximate state of charge can be determined from the following table: SPECIFIC GRAVITY AT 80°. DANGER. WEAR A FULL-FACE SHIELD WHEN WORKING AROUND A BATTERY BECAUSE OF THE DAN- GER OF AN EXPLODING BATTERY. BATTERY-EXPLOSIVE GASES. KEEP SPARKS, FLAMES, CIGARETTES AWAY. VENTILATE WHEN CHARGING OR USING IN AN ENCLOSED SPACE.
ALWAYS WEAR EYE PROTECTION WHEN WORKING ON OR NEAR BATTERY. INSTALLING THE BATTERY DANGER.
WEAR A FULL-FACE SHIELD WHEN WORKING AROUND A BATTERY BECAUSE OF THE DAN- GER OF AN EXPLODING BATTERY. BATTERY-EXPLOSIVE GASES. KEEP SPARKS, FLAMES, CIGARETTES AWAY. VENTILATE WHEN CHARGING OR USING IN AN ENCLOSED SPACE. ALWAYS WEAR EYE PROTECTION WHEN WORKING ON OR NEAR BATTERY. WARNING. IF THE BATTERY IS FROZEN OR THE CONTAINER IS BULGED, DISCARD BATTERY.
A FRO- ZEN BATTERY CAN EXPLODE. The frequency of recharging required will depend on the temperature of the storage area, but it is rec- ommended that the battery be monitored for state of charge every month.
Also, if the storage area is unheated in a cold climate and recharge is required, it is recommended that the area be heated to at least 60°F prior to charge. Ground Straps, Continued: NOTE. VEHICLES SERIAL NUMBER 9710-563353 AND GREATER DO NOT HAVE A GROUND PLATE UNDER THE VOLTAGE REGULATOR IN THE ELECTRICAL COMPONENT BOX. INSTEAD, A BRAIDED GROUND WIRE ATTACHES TO THE VOLTAGE REGULATOR MOUNTING BOLT AND GROUNDS TO THE VEHICLE FRAME AT THE SAME PLACE AS THE BATTERY GROUND. JAM NUT BRAIDED GROUND WIRE CUT-A-WAY. SECTIONS SECTION 13 - FE 290 ENGINE 13-18 GENERAL INFORMATION With the incorporation of the unitized transaxle on 1997 vehicles, engine rotation changed from counterclock- wise to clockwise. Although the change in engine rotation does not change service procedures in the Mainte- nance and Service Manual, a number of engine parts were changed.
General Information, Continued: 13-18 Camshaft: The lobes on the clockwise camshaft are arranged to operate in clockwise direction, and the shaft between the lobes is marked with a B as shown below. Crankshaft: The crankshaft for a clockwise engine has left-hand threads at the clutch mounting hole, and there is a machined groove in the outside diameter of the counterweight as shown below. ENGINE MOUNTING PLATE 13-18 On page 13-7 in the 1995-1996 Maintenance and Service Manual, the reference changes as follows: See Rear Suspension - Gasoline Vehicle, Section 18 in the 1997 Maintenance and Service supple- ment. INSTALLATION OF REMAINING ENGINE COMPONENTS On page 13-22 in the 1995-1996 Maintenance and Service Manual, step 7 under the heading above changes as follows: 7. 13-18 TYPICAL 2 PLACES FIGURE 14-6 ACCELERATOR ROD Accelerator Rod Removal On page 14-9 in the 1995-1996 DS Maintenance and Service Manual, under the sub-heading above, Figure 14-8 shows the previous accelerator pedal configuration as well as the current one. The revised Figure 14-8 at the top of page 139 shows only the current pedal configuration. 13-18 GASOLINE VEHICLES FIGURE 14-8 GOVERNOR CABLE The mounting of the governor and accelerator cables shown in the 1995-1996 Maintenance and Service Manual in Figure 14-11 on Page 14-12 was changed with incorporation of the unitized transaxle on 1997 vehicles.
The following instructions under the headings GOVERNOR CABLE and ACCELERATOR CABLE supersede those in the 1995-1996 Maintenance and Service Manual on pages 14-11 through 14-13. Removing the Governor Cable, Continued: 13-18 4. Remove the “E” ring (7) at the governor cable engine bracket (11), and governor cable transmission bracket (10) (Figure 14-11). Remove the spring cotter (9) and clevis pin (8) at the rear governor lever arm (Figure 14-11). 13-18 REFERENCE EXHAUST SECTION 9 FIGURE 14-11 3. Disconnect the cable (1) (Figure 14-11) from the cam in the electrical box (See Figure 14-9, Page 14- 10 in the Maintenance and Service Manual).
Remove the “E” ring (7) on the spring end of the cable at the accelerator cable bracket (5) (Figure 14- 11). MOVING PARTS! KEEP HANDS, CLOTHING, AND ALL OTHER OBJECTS AWAY FROM MOVING PARTS. DO NOT WEAR JEWELRY OR LOOSE CLOTHING.
SECTION 15 - EXHAUST SYSTEM See 1995 - 1996 DS Maintenance and Service Manual, Club Car Part Number 1019051-01. SECTION 16 - TORQUE CONVERTER GENERAL INFORMATION With the incorporation of the unitized transaxle on 1997 vehicles, the engine (and therefore the torque con- verter assembly) rotates clockwise. DRIVE CLUTCH DISASSEMBLY 13-18 FIGURE 16-5 Page 143. Drive Clutch Disassembly, Continued: 13-18 REMOVE THESE ITEMS FROM RIBS 10-24 SCREW FLAT WASHER DRIVE BUTTON DRIVE BUTTON TAKE UP SPRING RIBS FIGURE 16-8 DRIVE CLUTCH ASSEMBLY DRIVE BUTTON TAKE UP SPRING PROPERLY INSTALLED FIGURE 16-15 Page 144.
Step 13 on page 16-12 in the 1995-1996 Maintenance and Service Manual, under the heading DRIVE 13-18 CLUTCH ASSEMBLY, changes as follows: 13. Install the three drive button take-up springs (10) (Figure 16-5, Page 143) on the ribs of the clutch cover. OF THE DRIVEN CLUTCH, changes as follows: 6. Place the clutch assembly in a press and position the cam press tool (Club Car Part No. 1018091-01) on the cam as shown (Figure 16-21, this supplement). Hold the fixed face assembly and rotate the moveable face assembly (1) one third of a turn clockwise, then press the cam (2) onto the fixed face. Because the unitized transaxle, which takes the place of both the transaxle and transmission used on earlier gasoline vehicles, was incorporated in 1997 DS gasoline vehicles, Section 17 (and Section 9) in the 1995- 1996 DS Maintenance and Service Manual are superseded by Section 10 in this supplement.
SHOCK ABSORBERS 13-18 INSPECTING AND REMOVING SHOCK ABSORBERS 1. Check shock absorbers (7) for fluid leakage at the point where the shaft enters the shock absorber body. Replace leaking shock absorbers (Figure 18-1).
To remove a shock absorber, remove the nut (5), cup washer (9) and rubber bushing (10) from the stem at the top of the shock absorber (Figure 18-1). Remove the nut (5), cup washer (9), and rubber bushing (10) from lower mounting stem (Figure 18-1). Compress the shock absorber to remove it. INSTALLING SHOCK ABSORBERS 1.
To install, reverse the removal procedure. On the upper and lower shock absorber mounting stems, tighten the nuts until the rubber bushing expands to the size of the cup washer.
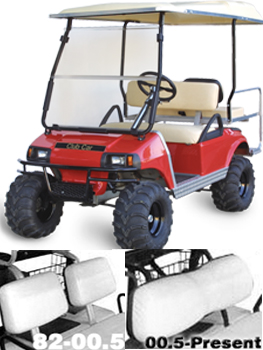
Removing the Mono-leaf Springs, Continued: 13-18 7. Remove the bolt (15) and nut (2) attaching the rear spring to the shackle (1) (Figure 18-1, Page 148). Remove the nut (2) and bolt (15) attaching the front of the spring to the vehicle frame (Figure 18-1, Page 148) and remove the spring. INSTALLING THE SNUBBER 13-18 1. To install the snubber, reverse the removal procedure. REFERENCE ENGINE SECTION 13 TYPICAL TYPICAL 4 PLACES 2 PLACES REFERENCE UNITIZED TRANSAXLE SECTION 10 FIGURE 18-4 Page 151.
13-18 Page 152. SECTION 19A - ELECTRICAL SYSTEM, 19-25 V-GLIDE 36 VOLT VEHICLE See Section 19A of the 1995 - 1996 Maintenance and Service Manual, Club Car Part Number 1019051-01. SECTION 19B - ELECTRICAL COMPONENTS, V-GLIDE 36 VOLT VEHICLE See Section 19B of the 1995 - 1996 Maintenance and Service Manual, Club Car Part Number 1019051-01. See Section 24 of the 1995 - 1996 Maintenance and Service Manual, Club Car Part Number 1019051-01.
SECTION 25 - TRANSAXLE, ELECTRIC VEHICLE For electric vehicles only, see Section 9 of the 1995 - 1996 Maintenance and Service Manual, Club Car Part Number 1019051-01. Disregard information pertaining to gasoline vehicles. SECTION 26 - REAR SUSPENSION, ELECTRIC VEHICLE See Section 25 of the 1995 - 1996 Maintenance and Service Manual, Club Car Part Number 1019051-01.
Golf Cars Club Car, Inc. Box 204658 Augusta, GA.
Club Car Factory Service Manuals for all Golf Carts, 1981 thru 2009 Club Car Factory Service Manuals for Carryall and Transportation Vehicles, 1998-2009 Please note: All Yamaha manuals are 'print-on-demand,' and shipped to you directly from the printer only via UPS GROUND. The lead time for this process is 3-5 business days for printing plus shipping time.SPECIAL NOTE. When selecting the shipping method you must choose UPS or additional shipping charges will be required and delay your shipment.